This is Part Three of our little project
- if you want to go back and check on something we did earlier, then click HERE.
The next time Smitty and I got together was
on Saturday, May 31st. It would be the last day for working in his metal fab shop because as far as the basic
assembly was concerned, we were sure to finish it up.
The first thing to work on were the banjos for the tool rests. I didn't want anything fancy but at the same time they needed to have enough pizazz to make them look like they weren't just thrown together. Here's what we came up with.
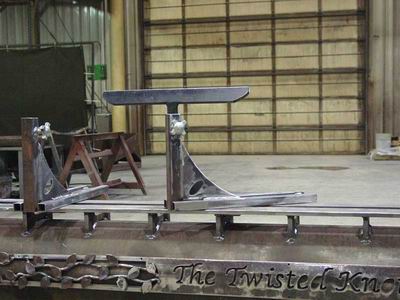
The knobs were ordered from Grainger's but I couldn't find any that had a stud, so I made do by cutting the heads off some bolts, threaded them into the knob then drilled a cross hole and secured them with a pin. We made two banjos because I have a vintage tool rest that is 36" wide with two posts. The tool rest you see above is 16" wide and I have two others; 12" and 6" wide, that I made 7 years ago. Here's a closeup of the other side of the banjo...
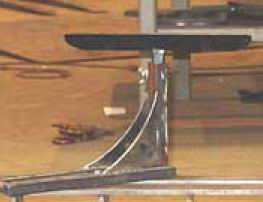
With that phase out of the way we turned our attention to making the housing for the headstock. Since I couldn't see any reason to purchase another motor and controller, I decided to use the DC motor from the lathe this new one will replace.
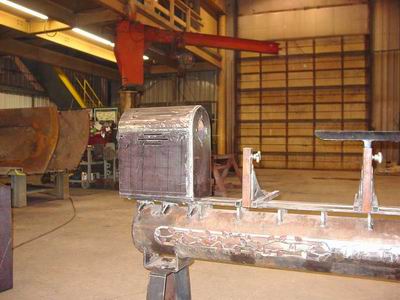
Smitty's shop doesn't have a machine for rolling metal so I came up with the idea of taking a piece of pipe and cutting it in half along its length. Next, we cut metal for the sides and front then Smitty welded it all together. Now, this is really odd, but if you were to meet him on the street he'd present no indication whatsoever he could even spell "weld" but let me tell you, that Smitty is a welding fool! I couldn't help but watch with admiration as he laid down a flawless continuous bead, which gave cause for me to place him right near the top of my list of heroes (be sure to let me know if I got that right, Ok Smitty?).
The headstock housing will completely enclose the motor and to prevent overheating we used the CNC plasma cutter to cut vent holes in the top of the sides and at the bottom of the rear cover. The rear cover will be bolted to angled tabs welded inside the housing.
While Smitty ran around like a mad man taking pictures, I took the opportunity to crack open a beer and stood back to admire our work...
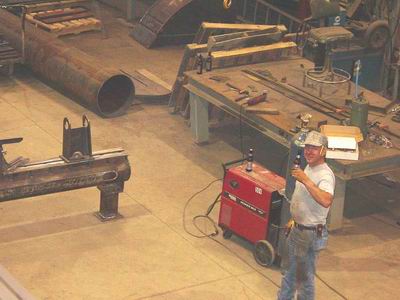
By now we'd pretty much worked ourselves out of a job and the only thing left to do was clean up the little dingleberries left by the welding process.
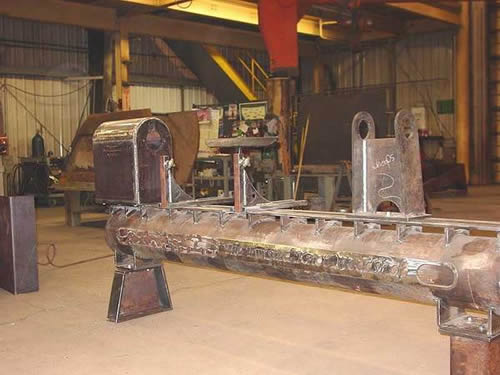
Judging from the smoke coming from Smitty's shoes, it looked like they were getting pretty warm so on his next pass I outstretched a bottle of beer, which forced him to come to a screeching halt - luckily near a convienent leaning spot.
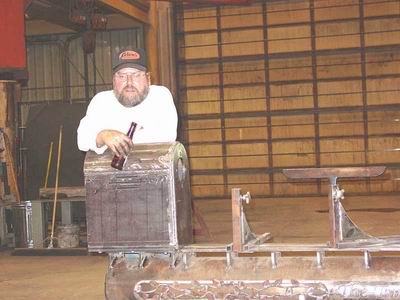
Here's a collage of shots from different angles...
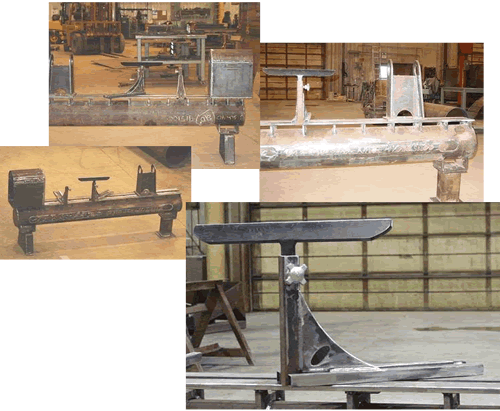
The next day Richie and I went to Missoula and hauled the new lathe to its new home here in the Mission Valley. I'll tidy up the welds by filling what few voids exist with body filler then paint it. Stay tuned for when I get around to doing that.
Thanks for looking! |